Top Guidelines Of Alcast Company
Top Guidelines Of Alcast Company
Blog Article
The 5-Minute Rule for Alcast Company
Table of ContentsThe 6-Second Trick For Alcast CompanyAlcast Company Can Be Fun For AnyoneIndicators on Alcast Company You Should KnowThe Only Guide for Alcast CompanyThe Best Strategy To Use For Alcast CompanySome Known Incorrect Statements About Alcast Company
The refined difference depends on the chemical material. Chemical Contrast of Cast Light weight aluminum Alloys Silicon advertises castability by reducing the alloy's melting temperature level and enhancing fluidness during spreading. It plays a critical function in allowing elaborate mold and mildews to be filled up properly. Additionally, silicon adds to the alloy's strength and wear resistance, making it useful in applications where durability is important, such as auto components and engine components.It additionally boosts the machinability of the alloy, making it much easier to process right into completed items. In this method, iron contributes to the total workability of light weight aluminum alloys.
Manganese adds to the toughness of aluminum alloys and boosts workability (aluminum casting company). It is commonly utilized in wrought aluminum items like sheets, extrusions, and profiles. The visibility of manganese aids in the alloy's formability and resistance to cracking throughout manufacture processes. Magnesium is a light-weight element that gives toughness and impact resistance to light weight aluminum alloys.
The smart Trick of Alcast Company That Nobody is Discussing
It enables the production of lightweight parts with superb mechanical properties. Zinc improves the castability of light weight aluminum alloys and helps manage the solidification process during spreading. It improves the alloy's toughness and solidity. It is commonly found in applications where detailed shapes and fine information are required, such as decorative castings and specific auto parts.
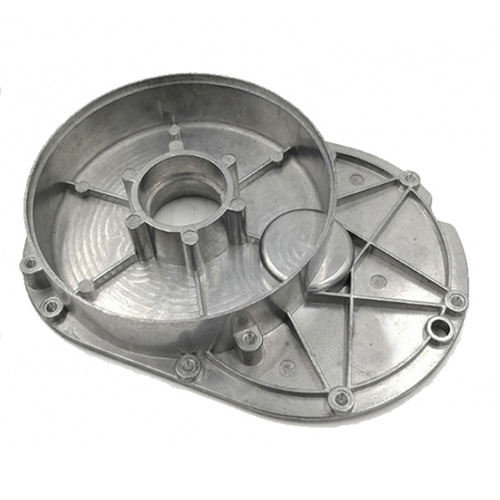
The key thermal conductivity, tensile strength, yield toughness, and elongation differ. Amongst the above alloys, A356 has the highest possible thermal conductivity, and A380 and ADC12 have the cheapest.
Alcast Company - An Overview
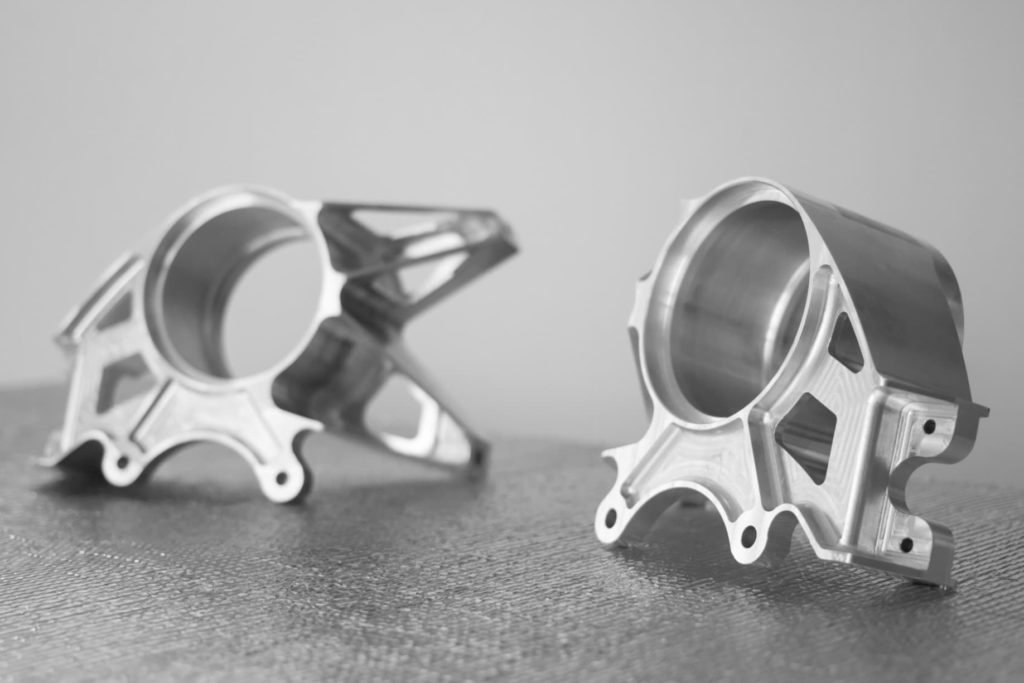
In precision spreading, 6063 is fit for applications where elaborate geometries and top notch surface area finishes are extremely important. Instances include telecommunication rooms, where the alloy's exceptional formability enables smooth and aesthetically pleasing designs while preserving structural honesty. Likewise, in the Lights Solutions industry, precision-cast 6063 components produce classy and efficient lights fixtures that call for intricate shapes and good thermal efficiency.
It results in a finer surface finish and much better rust resistance in A360. In addition, the A360 displays premium elongation, making it ideal for facility and thin-walled components. In precision casting applications, A360 is well-suited for markets such as Customer Electronics, Telecommunication, and Power Devices. Its boosted fluidness enables complex, high-precision parts like smart device casings and communication tool housings.
The Ultimate Guide To Alcast Company
Its special buildings make A360 an important selection for accuracy spreading in these sectors, enhancing product durability and quality. Aluminum alloy 380, or A380, is a commonly used spreading alloy with several distinctive qualities. It offers outstanding castability, making it an ideal selection for precision spreading. A380 exhibits good fluidity when molten, ensuring detailed and detailed mold and mildews are accurately duplicated.
In precision spreading, light weight aluminum 413 radiates in the Customer Electronic Devices and Power Tools sectors. This alloy's superior corrosion resistance makes it an outstanding selection for outside applications, guaranteeing lasting, sturdy items in the mentioned industries.
Not known Details About Alcast Company
When you have decided that the aluminum pass away casting process appropriates for your task, a critical next action is picking one of the most appropriate alloy. The aluminum alloy you select will significantly influence both the casting process and the homes of the final product. Due to the fact that of this, you should make your choice carefully and take an enlightened technique.
Determining the most appropriate light weight aluminum alloy for your application will certainly imply evaluating a wide array of qualities. These relative alloy attributes follow the North American Pass Away Casting Organization's guidelines, and we've divided them into 2 groups. The very first classification addresses alloy characteristics that affect the manufacturing process. The second covers qualities influencing the homes of the end product.
The Only Guide to Alcast Company
The alloy you choose for die spreading straight affects numerous facets of the casting process, like how very easy the alloy is to collaborate with and if it is vulnerable to casting defects. Warm fracturing, you could try here additionally called solidification breaking, is a normal die spreading issue for aluminum alloys that can result in interior or surface-level splits or cracks.
Certain light weight aluminum alloys are more prone to hot splitting than others, and your choice needs to consider this. One more usual problem discovered in the die casting of light weight aluminum is die soldering, which is when the cast stays with the die walls and makes ejection tough. It can damage both the cast and the die, so you need to try to find alloys with high anti-soldering buildings.
Rust resistance, which is already a noteworthy quality of light weight aluminum, can vary significantly from alloy to alloy and is an important characteristic to think about depending upon the ecological conditions your product will certainly be revealed to (Casting Foundry). Wear resistance is one more home frequently looked for in aluminum items and can set apart some alloys
Report this page